Understanding Gauge Glass Seals: Essential Insights for Business Success
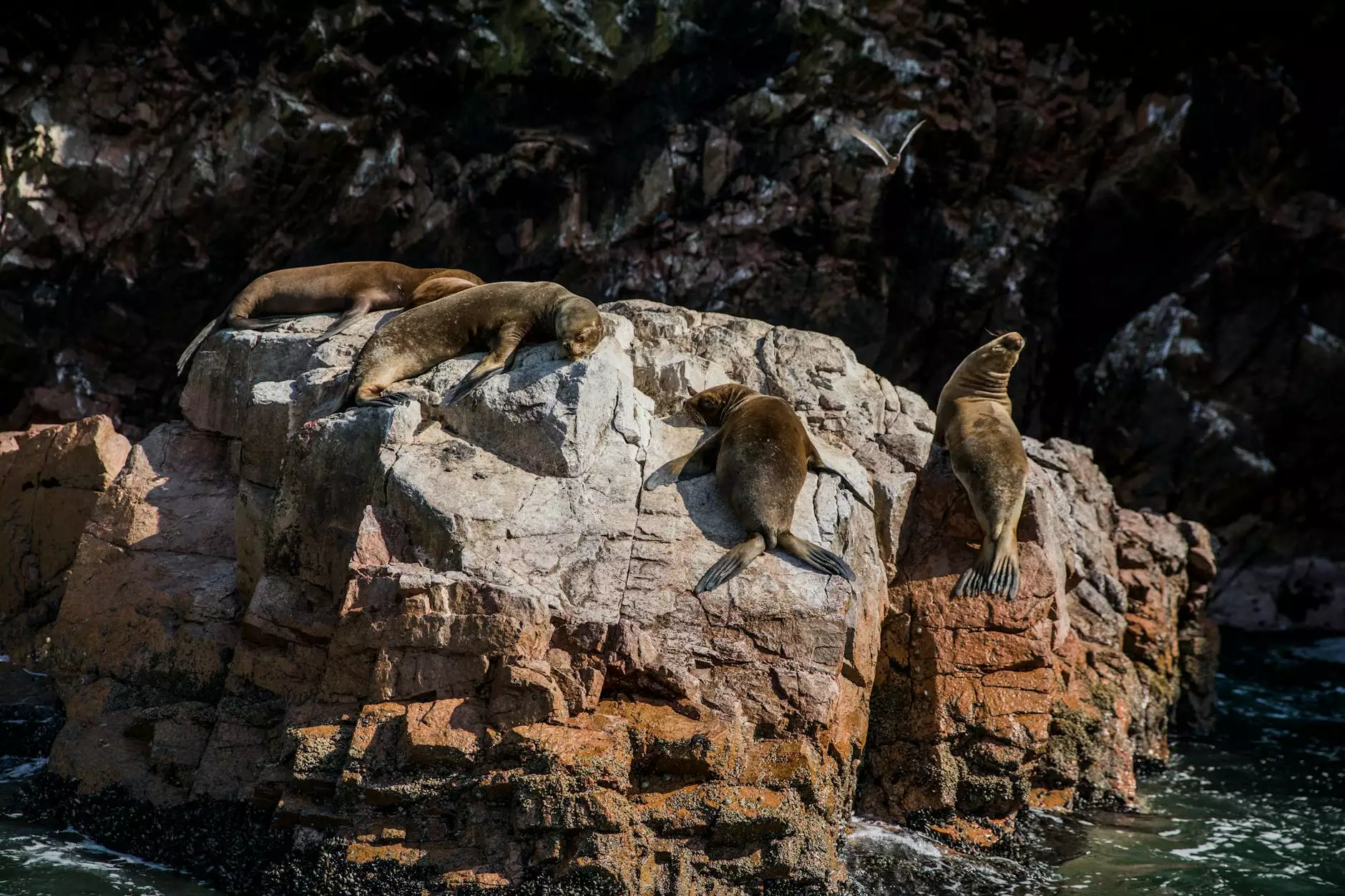
In the modern industrial landscape, where precision and reliability are paramount, gauge glass seals play a crucial role. These components ensure that measurements taken from various vessels, reactors, and tanks are accurate and reliable. In this comprehensive guide, we will delve into the intricacies of gauge glass seals, their applications, and the factors that influence their effectiveness in different environments.
What Are Gauge Glass Seals?
Gauge glass seals are specialized sealing devices used to secure the connection between a gauge glass and the vessel it is monitoring. Their primary function is to prevent leaks of liquid or gas while allowing for easy reading of the liquid levels. These seals are designed to withstand pressure and temperature fluctuations, ensuring operational integrity and safety in various applications.
The Importance of High-Quality Gauge Glass Seals
In industries such as manufacturing, oil and gas, and chemical processing, the integrity of gauge glass seals is vital:
- Safety: Leaks can lead to catastrophic failures and safety hazards.
- Accuracy: Accurate readings are essential for process control and efficiency.
- Durability: High-quality seals reduce downtime and maintenance costs.
Applications of Gauge Glass Seals
Gauge glass seals find extensive use in various sectors. Here are some of the primary applications:
1. Chemical Processing
In the chemical industry, gauge glass seals allow for the safe monitoring of corrosive and hazardous liquids. The materials used for seals in this sector must be resistant to these substances, ensuring long service life and reliability.
2. Oil and Gas
In oil and gas, gauge glass seals help in monitoring levels in tanks and separators. The extreme conditions present in these environments demand seals that can handle high pressures and temperatures.
3. Water Treatment
Water treatment facilities use gauge glass seals to monitor water levels in tanks. The ability to detect changes in level accurately is crucial for the efficiency of treatment processes.
4. Food and Beverage
In the food industry, compliance with hygiene standards is critical. Gauge glass seals here must be made of materials compliant with food safety regulations.
Features to Consider When Choosing Gauge Glass Seals
Selecting the right gauge glass seals can significantly impact the efficiency and safety of operations. Here are essential features to consider:
1. Material Compatibility
Ensure that the materials used in the seal are compatible with the fluids they will encounter. Common materials include:
- Rubber – Flexible and resistant to wear.
- PTFE (Teflon) – Excellent chemical resistance.
- Metal – Often used in high-temperature applications.
2. Temperature and Pressure Ratings
Different applications have varying temperature and pressure requirements. Always check the ratings to ensure the seals will perform under your operating conditions.
3. Size and Dimensions
The size of the gauge glass seal must match the specifications of the gauge and the vessel. Pay attention to:
- Diameter: The internal diameter should fit snugly against the gauge glass.
- Thickness: A thicker seal may be needed for high-pressure applications.
Installation Guidelines for Gauge Glass Seals
Proper installation of gauge glass seals is crucial for ensuring leak-proof operation. Here are some guidelines:
1. Surface Preparation
Before installing the seal, ensure that the surfaces are clean and free from debris. Any contaminants can compromise the seal integrity.
2. Alignment
Align the gauge glass and the vessel properly. Misalignment can cause uneven wear and potential leaks.
3. Torque Specifications
Follow the manufacturer’s torque specifications carefully. Over-tightening can damage the seal, while insufficient tightening can lead to leaks.
Maintenance of Gauge Glass Seals
Regular maintenance of gauge glass seals can prolong their life and ensure operational efficiency. Here are tips for maintaining them:
1. Regular Inspections
Regularly inspect the seals for signs of wear or damage. Look for:
- Cracking
- Discoloration
- Liquid or gas leaks
2. Cleaning
Keep the area around the gauge glass seal clean. Use appropriate cleaning agents that do not damage the seal material.
3. Replacement
Replace seals that show signs of wear promptly. Delaying replacement can lead to more significant issues down the line.
Common Issues and Solutions
Even with the best products, you may encounter issues with your gauge glass seals. Here are some common problems and potential solutions:
1. Leaks
If you notice a leak, first ensure the seal is tightened to the correct torque. If the issue persists, inspect for wear and replace if necessary.
2. Cracking
Cracking often occurs due to thermal expansion or improper material choice. Choose seals based on the anticipated conditions to mitigate this risk.
3. Difficulty in Reading Levels
If liquid levels are difficult to read, ensure there is no debris obstructing the gauge glass. Cleaning may resolve this issue.
Conclusion: The Future of Gauge Glass Seals
The importance of gauge glass seals in various industries cannot be overstated. As technology evolves, so do the materials and designs of these crucial components. Innovations in materials science are paving the way for more durable, heat-resistant, and chemically compatible seals. Whether in chemical processing, oil and gas, or food services, understanding gauge glass seals and ensuring their proper use and maintenance will lead to enhanced safety, efficiency, and productivity.
Investing in high-quality gauge glass seals is an investment in the overall success of your operation. By selecting the right materials, adhering to proper installation protocols, and maintaining these seals regularly, businesses can mitigate risks associated with leaks and inaccurate measurements. For further information and expertise, consider visiting gage-glass.com to explore a comprehensive range of products suited to your industrial needs.