Understanding Crankshaft Manufacturing in the Diesel Engine Parts Industry
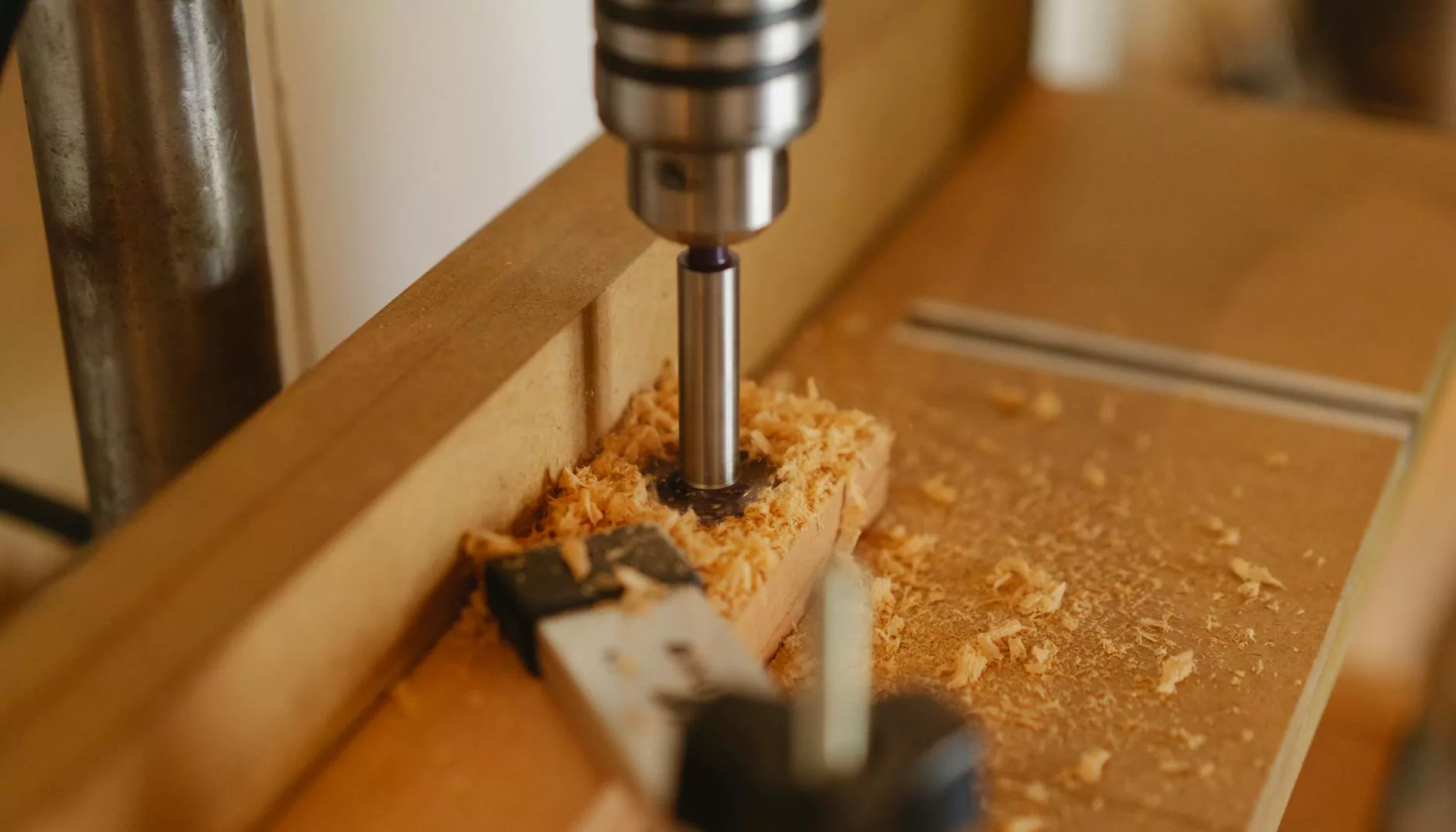
The crankshaft is one of the most critical components in any internal combustion engine, especially in diesel engines. Its primary function is to convert the oscillating motion of the pistons into rotational motion, which ultimately drives the vehicle or machinery. This article delves into the crankshaft manufacturing process, the significance of quality in diesel engine parts, and what to consider when sourcing spare parts from suppliers like client-diesel.com.
The Importance of Crankshafts in Diesel Engines
A crankshaft serves several vital functions in the operation of a diesel engine:
- Converting Energy: It converts the linear motion of the piston into rotational energy, making it a crucial part of the engine's functionality.
- Balancing Forces: Well-manufactured crankshafts balance the forces generated during combustion, ensuring smoother engine operation.
- Durability: Quality crankshafts are designed to withstand extreme conditions, including high temperatures and pressures, typical in diesel engines.
Overview of the Crankshaft Manufacturing Process
The manufacturing of crankshafts is a complex process that requires precision engineering, state-of-the-art machinery, and the right raw materials. Below are the primary steps involved in crankshaft manufacturing:
1. Raw Material Selection
Choosing the right raw materials is fundamental for producing high-quality crankshafts. Typically, steel alloys such as forged steel or cast iron are selected based on their durability and ability to withstand stress.
2. Forging and Casting
In this stage, the raw materials are shaped into rough crankshaft forms. Forging processes, where metal is shaped under high pressure, are often preferred due to the superior strength these methods provide. Casting can also be used, in which molten metal is poured into molds.
3. Machining
After the crankshafts are forged or cast, they require precision machining. This step ensures that the crankshafts meet exact specifications, with tight tolerances that are crucial for performance.
Machining involves several operations:
- Turning: Creates precise cylindrical shapes on lathes.
- Milling: Removes material from the crankshaft to create flat surfaces.
- Grinding: Produces smooth finishes on critical bearing surfaces.
4. Heat Treatment
Heat treatment is essential for enhancing the mechanical properties of the crankshaft. This process involves heating the crankshaft to specific temperatures and then cooling it under controlled conditions, which increases its strength and resistance to fatigue.
5. Surface Finishing
The final surface finishing is crucial not only for aesthetics but also for performance. Options include polishing, which reduces friction, and coating treatments that improve corrosion resistance.
Quality Assurance in Crankshaft Manufacturing
In the crankshaft manufacturing industry, ensuring the quality of the product is paramount. Various testing methods are employed to ensure each crankshaft meets rigorous standards:
- Dimensional Inspection: Ensures all measurements are within specified tolerances.
- Non-Destructive Testing (NDT): Techniques like ultrasonic testing or magnetic particle inspection are used to check for internal flaws without damaging the crankshaft.
- Tensile Testing: Assesses the strength and ductility of the crankshaft material.
Common Issues in Crankshaft Failure
Understanding potential failures in crankshafts can help manufacturers improve their processes and ensure that the end product is reliable. Some common issues include:
- Fatigue Cracks: Occur due to repeated stress cycles and can lead to catastrophic failure.
- Corrosion: If surfaces are not properly treated, environmental exposure can lead to rust and degradation.
- Misalignment: Poor installation or component defects can cause uneven stress distribution, leading to early failure.
Sourcing Quality Crankshafts from Suppliers
When looking for crankshaft manufacturing suppliers, particularly for diesel engine parts, consider the following factors:
1. Reputation and Experience
Select a supplier with a proven track record of delivering quality products. Research their history and client testimonials to gauge their reliability.
2. Compliance with Standards
Ensure that the supplier adheres to international quality standards such as ISO 9001. This compliance indicates a commitment to quality management and assurance.
3. Range of Offering
A good supplier should provide a comprehensive range of crankshafts tailored for various diesel engine models, ensuring that you find the right part for your specific needs.
4. Customer Support
Consider suppliers that offer excellent customer support. They should be available to answer any technical questions and help with identifying the right parts.
Future Trends in Crankshaft Manufacturing
The crankshaft manufacturing landscape is evolving, driven by technological advancements and the push for greater efficiency. Here are some trends shaping the future of the industry:
1. Automation and Advanced Robotics
The integration of automation in manufacturing processes can significantly increase efficiency and reduce human error, leading to higher quality crankshafts. Robotics can assist with precise machining and finishing tasks.
2. Additive Manufacturing
3D printing or additive manufacturing is poised to revolutionize crankshaft production. This technology allows for the creation of complex geometries that are otherwise difficult or impossible to achieve through traditional methods.
3. Sustainable Practices
As industries move towards sustainability, crankshaft manufacturers are likely to adopt eco-friendly practices. This includes recycling materials and reducing waste during production.
4. Enhanced Materials
The development of new materials with superior properties is another trend. Innovations in metallurgy can lead to crankshafts that offer better performance, reduced weight, and improved resistance to wear and fatigue.
Conclusion
In conclusion, crankshaft manufacturing is a vital aspect of producing reliable and high-performing diesel engines. The intricacies of the manufacturing process, the importance of quality assurance, and understanding the common issues that can lead to failure are essential for both manufacturers and consumers alike. As the industry moves forward, keeping an eye on emerging trends and technologies will be crucial for maintaining competitiveness and ensuring longevity in the market.
For those seeking to procure quality diesel engine parts, consider partnering with established suppliers like client-diesel.com. Their commitment to quality and range of offerings ensures you find the right solutions for your engine needs.